
For this project I decided to try a two part silicone mold. Although it takes a little more time and planning to make the mold this way, it will make my life a lot easier when it comes to casting and demolding because I can remove the mold in pieces. In preparation for pouring the first half of the silicone, I need to build a clay dam to stop the liquid silicone from covering the entire helmet.

The dam is essentially defining the boundaries of the mold…any portion of the sculpt I don’t want cast is walled off, including the bottom. The clay is sulfur-free, sulfur based clay would inhibit the curing of the silicone.

The finished clay dam.

In this photo you can see clearly where the seam will bisect the final mold.

I used Smooth-On’s Rebound 25 brushable silicone for this mold. I progressively build up the mold with layer upon layer of silicone until I have a thick, uniform coating of rubber. The first layer you see here is called a print coat. I’ve diluted the silicone so that the layer is very thin…this prevents air bubbles from forming, which would ruin the surface detail that this coat is intended to capture.

The mold after about three coats of silicone.

After about five coats of silicone I was pretty happy with the thickness of the mold. The little half spheres are registration keys made of hardened silicone, they will ensure that the silicone mold “locks” into the mother mold correctly every time I assemble the mold for casting.

Once the silicone on the first half is cured, I can turn the sculpt right side up and remove the clay dam.

Here I’ve trimmed off all the excess silicone around the edges of the mold and have added more registration keys. These keys will ensure that the two halves of the silicone mold lock into each other correctly.

The bottom of the sculpt needs to be walled off on this side too in preparation for pouring the second half of the mold.

Silicone doesn’t stick to anything except itself. In order to prevent the second half of the mold from fusing with the first, I coated the exposed rim of the mold with sealing wax. I masked the sculpt so that wax didn’t get on it…I DO want the silicone to stick to THAT!

The print coat for the front half.

Filling in the recessed areas with silicone.

The front half after about four coats.

The finished two part mold with registration keys on both halves.

Silicone rubber is excellent for capturing detail, but you can’t stop there because a silicone mold by itself is too flexible to cast into. You need a hard jacket to surround the mold so it keeps the correct shape during casting. This is the frame for my mother mold made from ¼ inch mdf. My mother mold will be a three part jacket that bolts around the assembled silicone mold.

The backside of the frame. The back of the mother mold will split in two, while the front will remain whole.

The completed mother mold. I used Smooth-On’s Plastipaste to make the outer shell. Plastipaste is a fibrous brushable plastic that is very hard and rigid when cured, which makes it ideal for a mother mold. It’s also HEAVY.

The back of the mother mold. The whole assembly is held together with the bolts and wingnuts that join the frame.
Once the mother mold cured I was able to remove the sculpt. Here is the disassembled mother mold with the front and two halves of the back.
The back halves of the mother mold joined together.
Silicone molds inserted into the two halves of the mother mold.
The assembled mold showing the negative left by the sculpt!

I slush cast a few helmets using a couple different resins as tests, ultimately I decided to use polyester resin reinforced with fiberglass. Like the film helmet, my helmet is supposed to fit very closely to the wearer’s head, so I wanted to get my pulls as thin as possible so that they would be comfortable. Fiberglass allowed me to make castings that were thin, lightweight and strong. In this photo I have just finished fiberglassing the interior of one of my castings.

The finished castings require a little bit of touching up to eradicate the mold seam and stray air bubbles.


Two of my fiberglass castings sitting next to each other. Once I’ve taken care of the detailing, I remove the piece in front with a dremel tool. After some sanding and priming, they’re ready for paint!

Due to time constraints, I finished the helmet with off-the-shelf autobody spray paints. I did a couple of tests to get the right colors, and generally I’m pretty pleased with the results. Here I have the first coat of metallic carbon gray masked and ready for the silver trim.

Masking this thing took a while, but was worth the effort!

Some shots of the finished helmet. The silver should be more metallic and I skimped on the black inking that lines the border of the trim and feathers into the gray, but I am really pleased with the overall look!


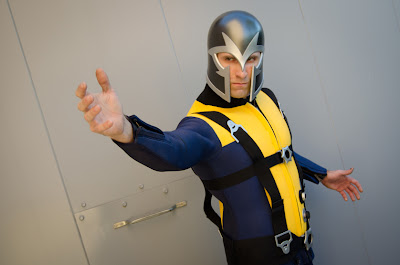
The finished costume for Halloween '11...thanks from taking a look!
7 comments:
That guy in the last picture is a Hotty McHotty Pants.
Pretty talented too.
Very cool
Nice post!
programming tutorials
Wow, that´s very nice art!
You should come to PAX PRIME with your soldier costume... I'll be there as a medic.
You have the mold I'll buy an unfinished casting & pay for the shipping and handling. Let me know.
Post a Comment